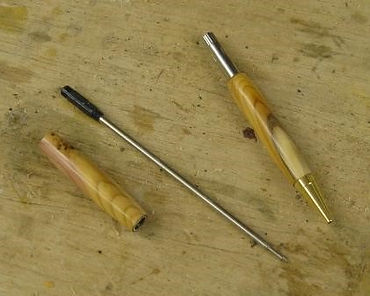
Completed prior to assessmbly

Example pen kit
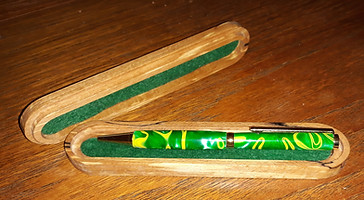
Pen making requires very little additional kit. A mandrel like the one below is absolutely necessary and they come to fit both 1MT and 2MT sizes for different lathes (there are MT converters available as well). You only need a fairly small lathe.
The most common pen internal diameter is 7mm - often called streamline, slimline or comfort pens - these kits can cost from under £2.00 upwards to over £3.00. Other more complex and fancier pen kits can cost up to £20.00.
They are all constructed in a similar way - blanks are cut to length and drilled lengthwise on a drill press or lathe to suit the size and diameter of the brass tubes supplied with the kit. The tubes are glued into the blanks and then the ends trimmed to fit. The tubes with blanks attached are then inserted onto a mandrel and put on the lathe. The wood is turned down to fit and then sanded and finished. Once dried the whole pen is assembled.
It took a while to find the best finish to put on pens. Initially I was using a coat of sanding sealer and then friction polish followed by carnuba wax and although this gave a fine and polished finish, when the pens were used over time the oils in the fingers caused the polished surface of the pens to dull somewhat. I read on the net about the use of superglue finish and this is what I always use as standard now. I buy the sets of small tubes of superglue from Poundstretchers or similar as they are very cheap and I tend not to waste any in open tubes. Two tubes does maybe 3 pens. After putting on say 5 or six coats of superglue I sand it down from 400 upwards to 1200 grit and lastly polish with T-Cut (car paint restorer which has a very light abrasive and polish action).
In terms of sanding before applying the polish I tend to start at 120 or 180 dependant on the surface and go through the grades 180, 240 or 320 - no point going further as I am then applying the superglue. After at least 5 coats of superglue I sand again up to 1200 grit and then use micromesh to go to 15000. Finally polish with T-cut.
I have tried a number of materials apart from normal wood blanks including acrylic, coloured layers of ply and most recently corian. Corian works very well if you treat it as a hard wood - after turning I just run through the grits again up to 1200 and then polish again with T-Cut. One problem is that corian is not made in sheets more than 3/8th of an inch apart from white so there is a bit of a chore lapping two pieces together and then gluing then to make a blank of sufficient thickness to drill. The way Corian is made means that there is a gradient of mineral chips in the material and to avoid showing a line between two glued up sections you need to glue top to top.



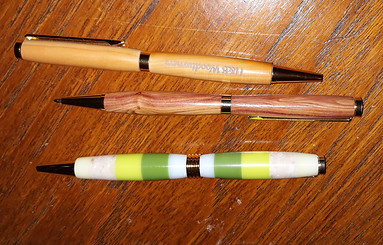

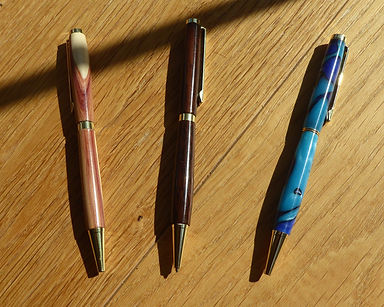
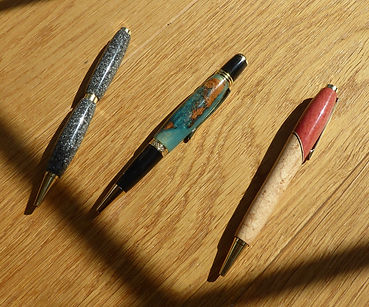
